A week ago our founder, Fahad Awadh travelled to Taiwan and Korea to visit equipment manufacturers and suppliers. Fahad had a chance to test a roasting production line from a company based in Kaohsiung, Taiwan. This particular production line is used to add value to products like cashews and peanuts by roasting and seasoning. Taiwan is well known for its high-quality manufacturing sector. This particular company has more than 50 years experience in manufacturing of food processing equipment. Taiwan is also home to Apple’s largest iPhone subcontractor, Hon Hai Precision Industry also known as Foxconn Technology Group. The country has excellent infrastructure; a high-speed rail reduces travel time between cities.
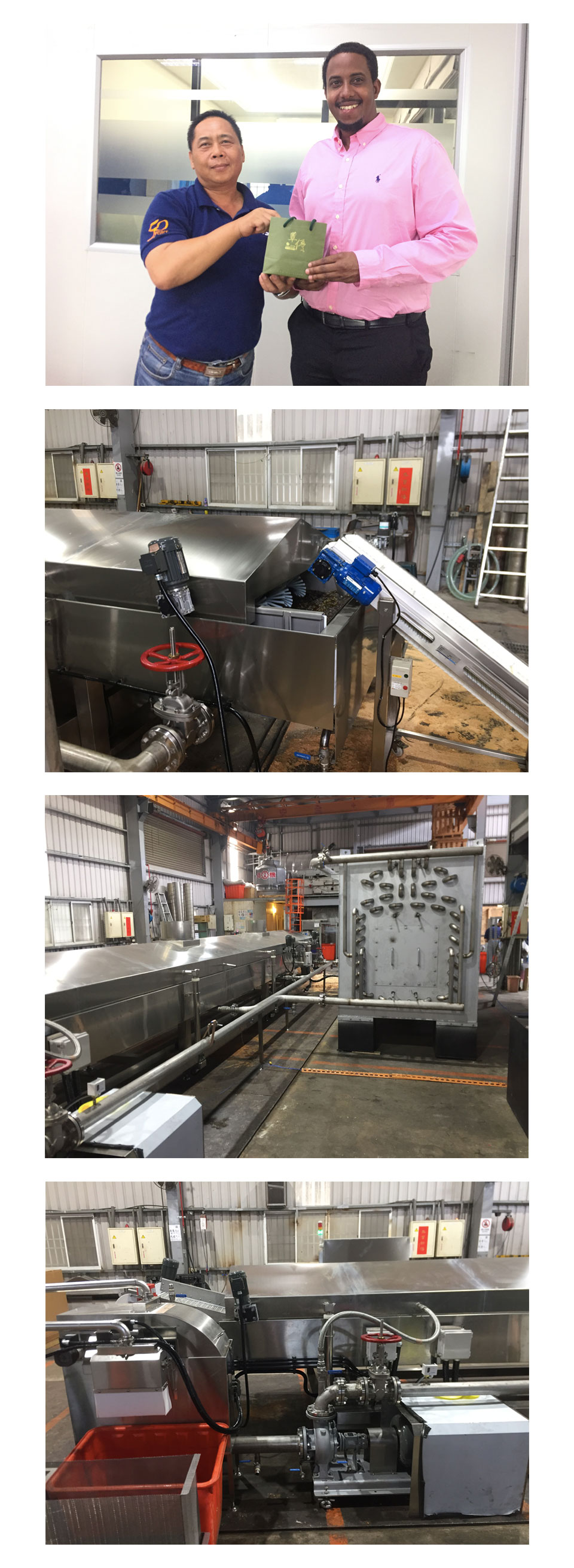
Fahad also had a chance to visit a packaging equipment manufacturer in Taichung, Taiwan. This company specializes in cup filling and sealing machines. In addition they also manufacture pouch-filling equipment for nuts and snacks.

In Seoul, South Korea, Fahad had a chance to visit a packaging materials manufacturer and other factories that make up the packaging value chain. This company in South Korea is a supplier of packaging materials to blue chip companies such as Starbucks and Wal-Mart. With a HACCP, ISO-22000 certified production facility they produce the highest quality packaging materials for both domestic and export markets. Their facility houses a 10 color gravure film printing production line; including embossing, lamination, gluing, slitting, pouch making and die cutting. Seoul has a vibrant packaging industry with all the raw materials being produced locally. The packaging materials are FDA approved food grade materials. Fahad had a chance to visit other facilities that produce the film used in the manufacture of the packaging as well as the gravure cylinder production. He also had a chance to visit other packaging equipment manufacturers; Seoul has a vibrant manufacturing industry. With many of these manufacturers having the equipment to machine stainless steel components on-site.
At YYTZ we practice the principle of Genchi Genbutsu; learned from Toyota Motor Corporation, which means going to source and understanding for your-self. By visiting our suppliers’ facilities and understanding the value chain in which they operate in, we are able to understand the quality of the production process. This leads to an understanding of the quality parameters that are employed to ensure the finished product is of the highest quality.
Below we will showcase the plastic packaging value chain. We will start with photos of the printing and finishing facility. We will show you photos of the film making process, which provides the film to the printing and finishing facility. We will also show you the process of producing the cylinders that are used to transfer the ink to the film as per the design. As we mentioned that the production line can print 10-colors per label, each color will have its own cylinder. In order to have a vibrant packaging industry it is necessary to have companies serving each segment of the value chain, this enables a company to have access to the necessary raw materials. There is a synergy that is formed between all actors in the value chain, as a result the customer benefits from a high quality product and shortened lead times.
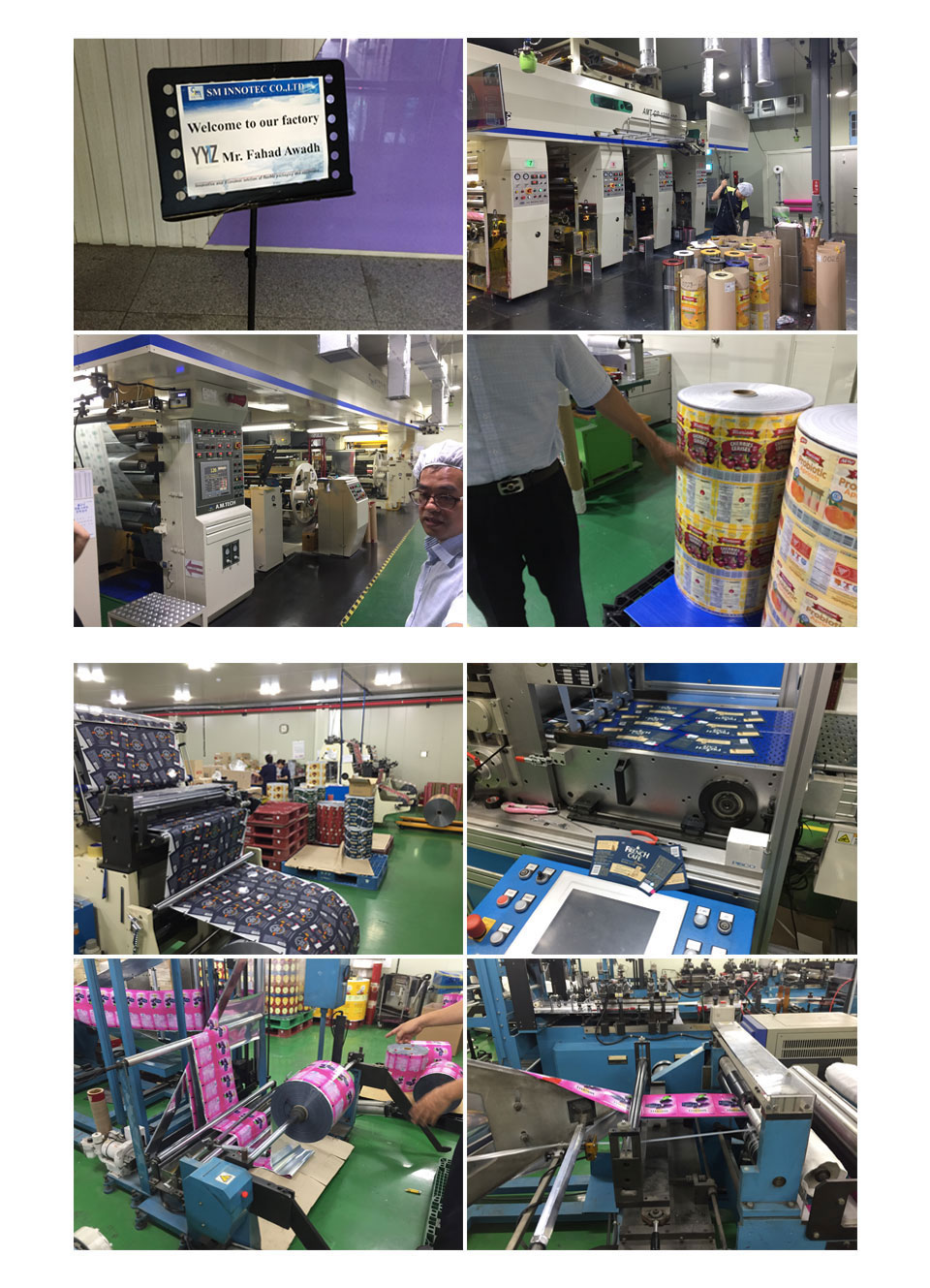
Photos 1-4 (clockwise): welcome sign, film is printed on these large 10-color printing lines, the next stage is lamination where film is laminated to aluminum foil and other u/v or matte gloss is applied, film is completed in rolls with two pouches per line (front and back).
Photos 5-8 (clockwise): printed labels are ready for die-cutting, cut labels are stacked and prepared for in-mold label application, pouches are being folded, glued and cut.
Gravure Cylinder Production
In Gravure printing, the first step is to create the cylinder with the engraved images that need to be printed: the engraving process will create on the cylinder surface the cells that will contain the ink in order to transfer it to the paper. Since the amount of ink contained in the cells corresponds to different color intensities on the paper, the dimensions of the cells must be carefully set: deeper or larger cells will produce more intense colors whereas smaller cells will produce less intense ones.
The Gravure cylinders are made of steel and plated with copper, though other materials, e.g. ceramics can also be used. The desired pattern is achieved by engraving a diamond tool. Following engraving, the cylinder is proofed and tested, reworked if necessary, and then chrome plated. The process takes two days to complete one cylinder.
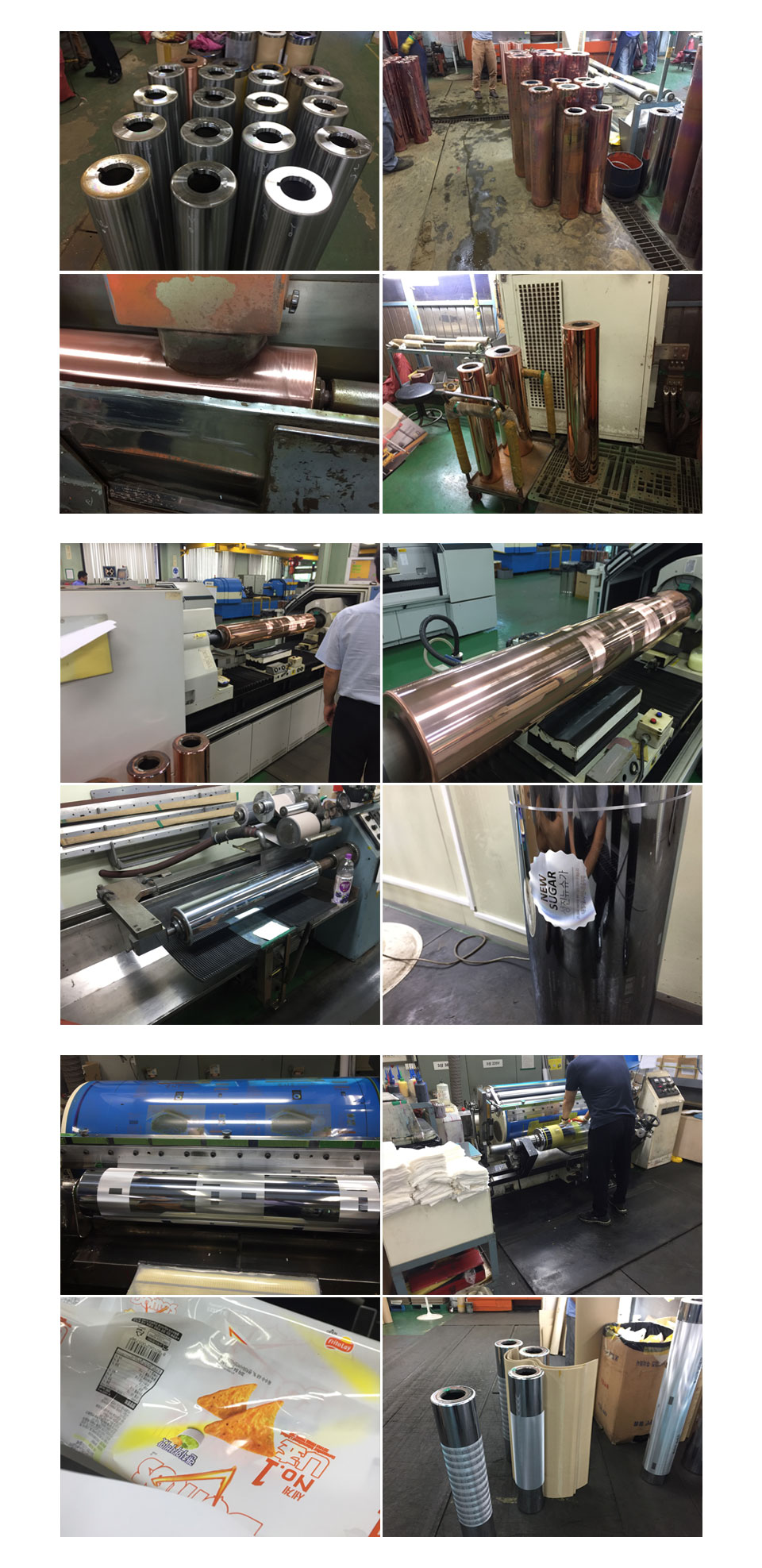
Photos 1-4 (clockwise): steel cylinders are ready for copper plating, cylinders have been copper plated, grinding is performed 3 times on the copper plated cylinders, cylinder is now ready for diamond engraving.
Photos 5-8 (clockwise): copper plated cylinders are placed in the diamond-engraving machine where the artwork is engraved onto the cylinder, cylinders are plated with chrome and grinding is performed to provide a smooth surface, cylinder is ready for proofing with ink.
Photos 9-12 (clockwise): cylinders are placed in a gravure printing press to test the colors and ensure the ink as applied as per design, a proof for a Dorito’s chips design, cylinders are prepared for shipment to printing facilities.
Polyethylene Film Production
Blown film extrusion is a technology that is the most common method to make plastic films, especially for the packaging industry. The process involves extruding a tube of molten polymer through a die and inflating to several times its initial diameter to form a thin film bubble. This bubble is then collapsed and used as a lay-flat film or can be made into bags. Usually polyethylene is used with this process, and other materials can be used as blends with these polymers.
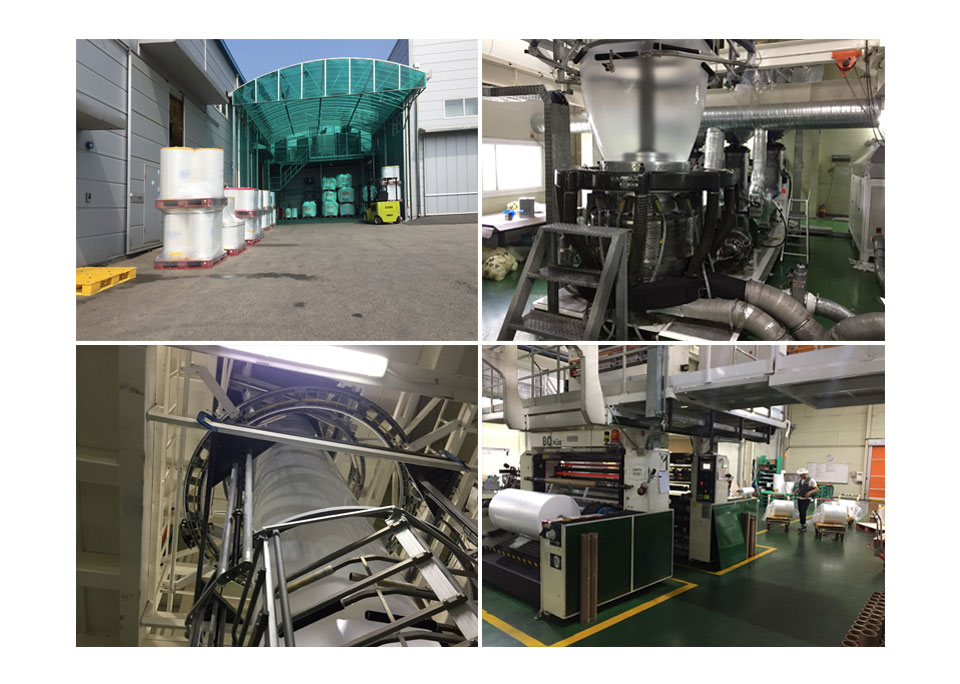
Photos 1-4 (clockwise): film production facility, polyethylene pellets are melted and air is blown to form a thin film bubble, the bubble is pulled continually upwards from the die and a cooling ring blows air onto the film, this reduces the temperature inside the bubble, while maintaining the bubble diameter, the film is finally passed through nip rollers to wind up rollers.
Fahad had an excellent trip and was able to experience the vibrant Korean industrial sector, where entrepreneurship is thriving. He ended the day with a Japanese sushi dinner with his hosts. While discussing the future co-operation between our two companies, they shared that Mount Kilimanjaro is very famous in Korea. ‘The Leopard of Mt. Kilimanjaro’ is a very famous Korean song; they were very excited to learn that we are based in the land of Mt. Kilimanjaro.
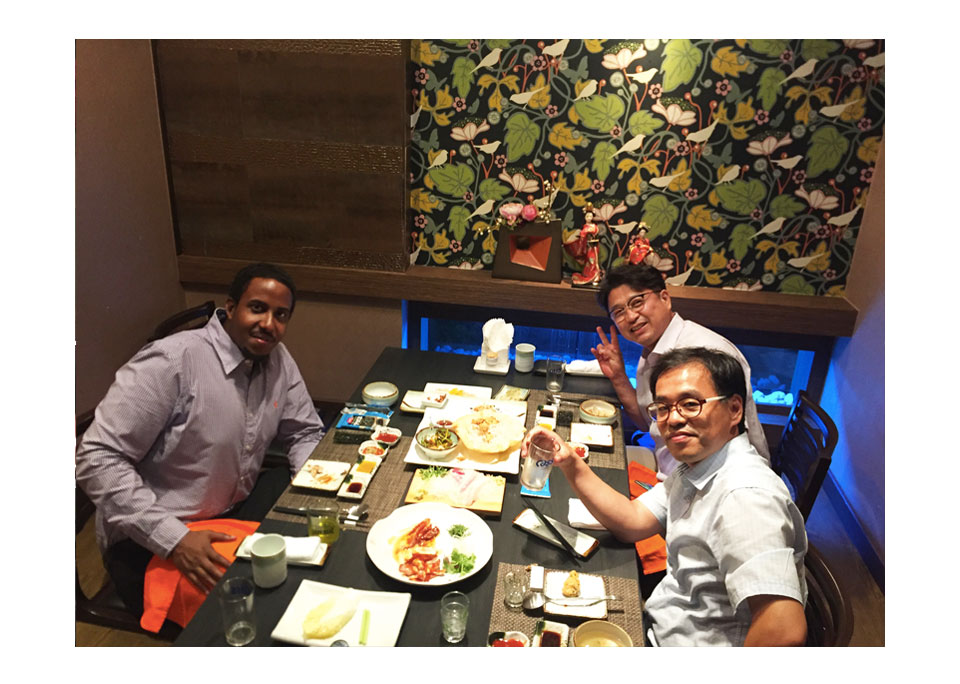
Photo: Fahad Awadh having a Japanese sushi dinner with his gracious Korean hosts.